INDUSTRIAL LUBRICANT
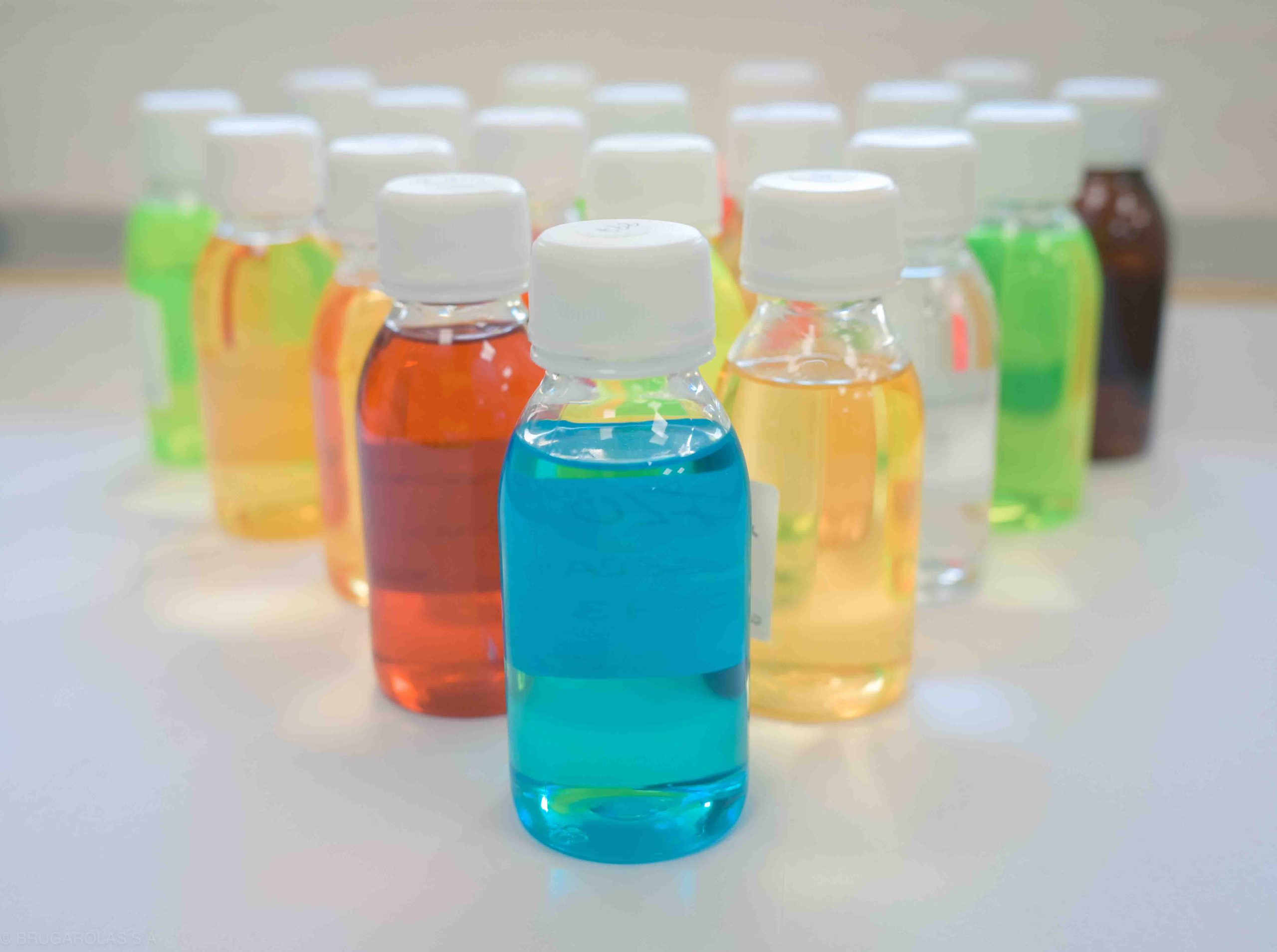
Introduction of
Industrial Lubricants
Industrial lubricants are designed to provide protection to machinery and workpieces when facing challenges such as moisture, loads, high speeds, and high temperatures. We offer a variety of lubricant formulations tailored to meet the stringent requirements of bearings, open and enclosed gearboxes, including products designed for food-grade or high-pressure applications. Whether it’s for generating and transmitting energy, reducing or transferring driving forces, cooling or compressing air, CNC machining applications, or numerous other production fields, industrial lubricants play a crucial role in influencing performance.
It’s important to note that many environments require the use of specialized lubricants to ensure on-site safety and proper machinery operation. Eagle Brand industrial lubricants optimize equipment performance, extend oil change intervals, and reduce energy consumption (at specific lubrication points). Additionally, our Ecolabel-certified and biodegradable lubricants contribute to your journey towards ESG sustainability.
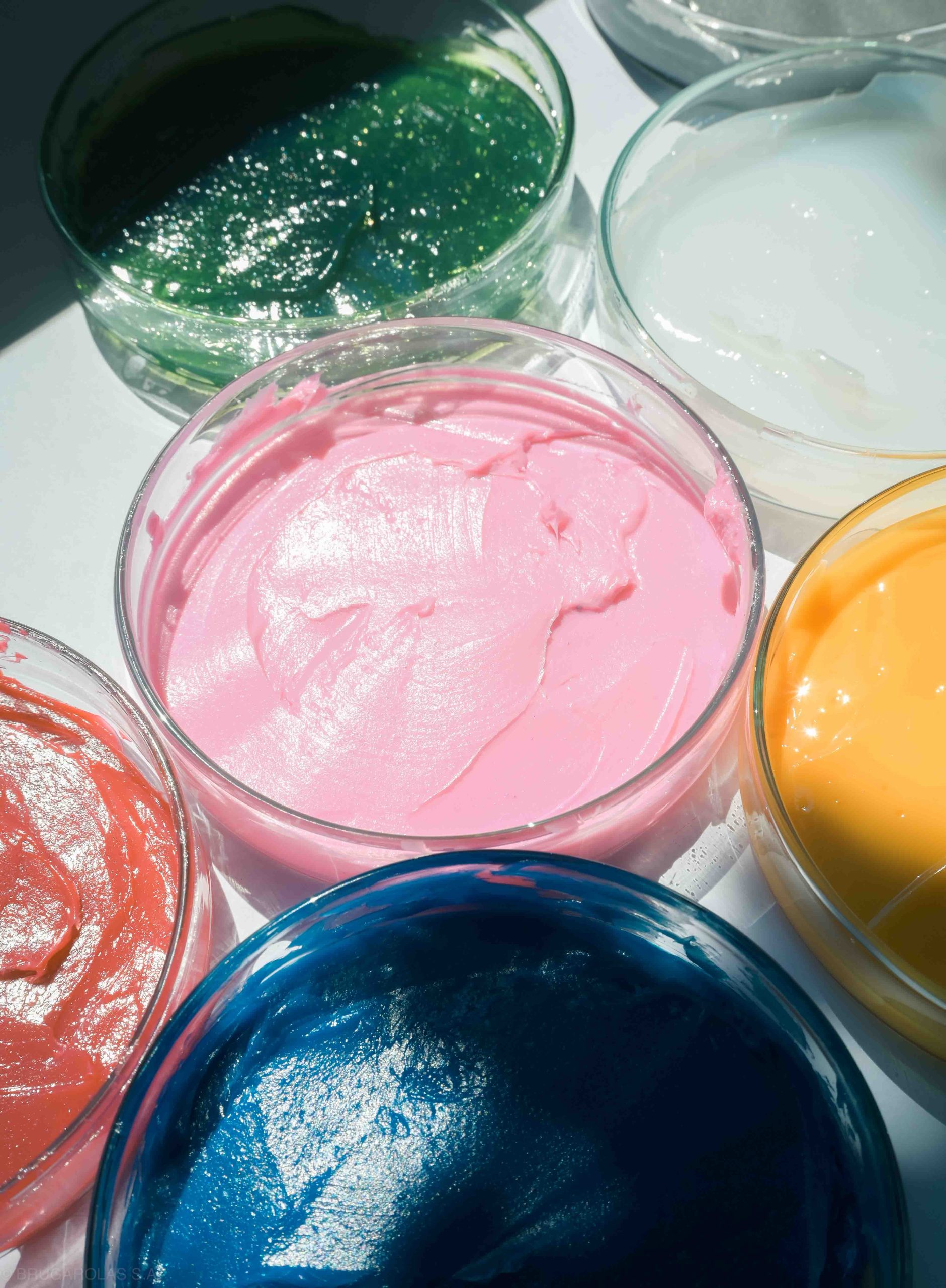
Introduction of
Grease
The key distinction between lubricating oil and lubricating grease lies in the inclusion of soap (thickener) in grease. Grease possesses superior mechanical stability, high drop point, high load-carrying capacity, reduced wear, and excellent water resistance and corrosion protection properties.
Advantages of lubricating grease include:
- No need for complex sealing components and oil circulation systems, allowing for simplification of bearing size and overall equipment, enabling smaller and more streamlined designs.
- A long-lasting effect, requiring less frequent replenishment, particularly beneficial for friction components that are difficult to maintain.
- Good adhesion and sealing properties. Preventing the ingress of water and dust.
- Providing enhanced protection to metal surfaces. Grease also has a broader temperature usage range compared to lubricating oil.
Potential disadvantages of lubricating grease are:
- Grease is a semi-fluid substance and can be less flowable at room temperature. This makes changing grease on components more challenging, and bearing cleaning can be cumbersome, often requiring partial or complete disassembly.
- Incorporated water, dust, and debris are difficult to remove from grease.
- Greater resistance can lead to poorer heat dissipation and cooling capabilities.
- The suitability of grease or oil depends on the equipment’s condition and the specific lubrication points.
Benefits
The purpose of using lubricants
Reduce Wear
Oil and grease reduce wear by providing a protective lubricating film between surfaces in motion, preventing direct metal-to-metal contact.
Protect Components (Anti-corrosion, anti-oxidation)
Lubricants protect against oxidation and corrosion through the use of additives and by creating a protective barrier on metal surfaces.
Minimize Friction
By lubricating surfaces, grease lowers friction, which in turn reduces heat generation—excessive heat can accelerate wear and material degradation.
Inhibit Rolling Contact Fatigue
Rolling Contact Fatigue (RCF) is a type of surface and subsurface damage that occurs in rolling elements (such as bearings, gears, and cam followers) due to repeated cyclic stress. Lubricants help inhibit RCF.